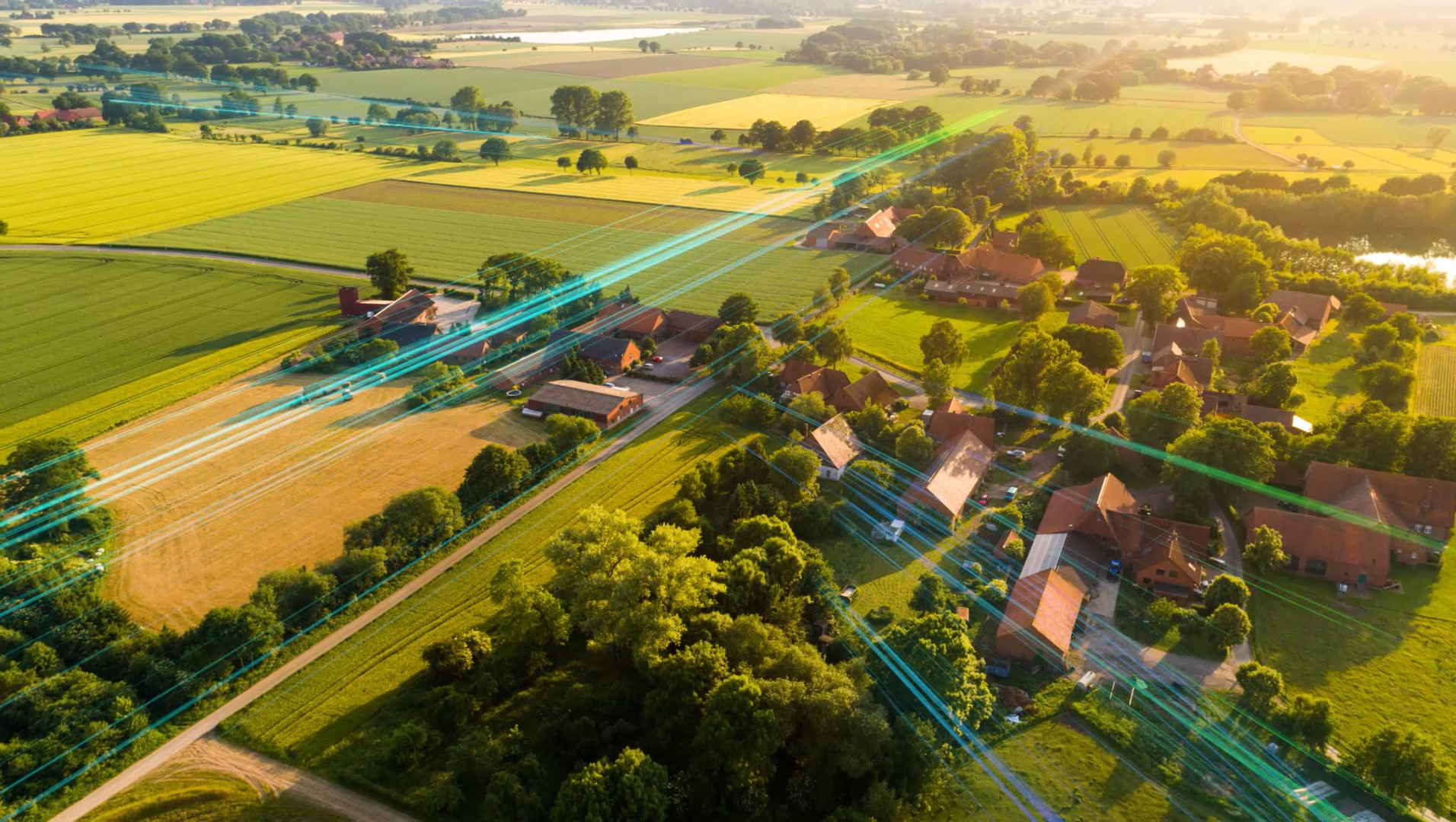
Innovation fördern
Zukunft gestalten
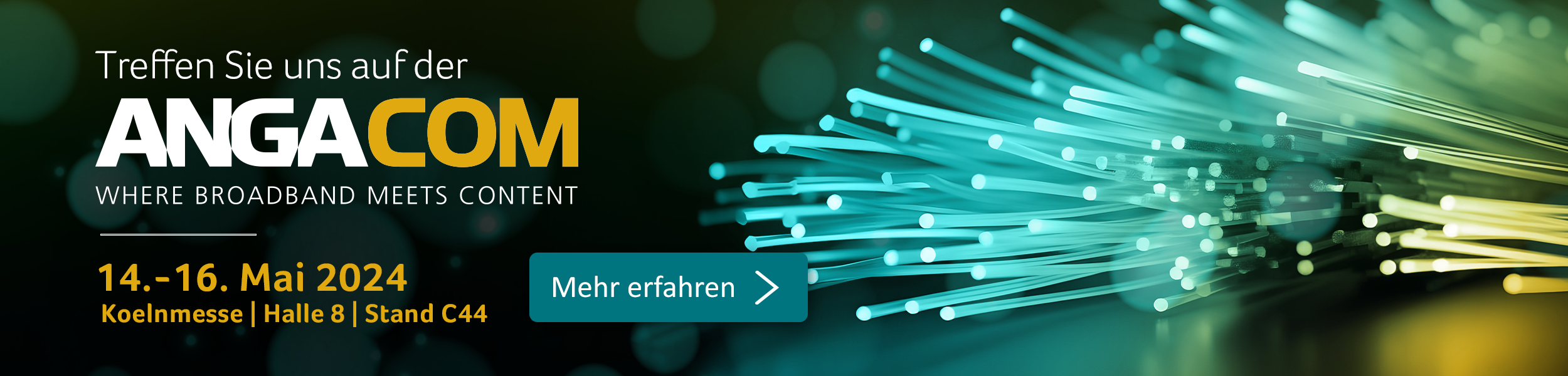
Infrastrukturen
Im ländlichen Raum das volle Potenzial für Wirtschaft und Gesellschaft ausschöpfen – mit nachhaltigen Infrastrukturen.
Transformation
Ob Evaluation des Ist-Zustandes, Strategieentwicklung oder Umsetzung von Digitalisierungsprojekten – wir unterstützen bei der digitalen Transformation.
Dienstleistungen und Produkte
Mit individuellen Lösungen und nachhaltigen Innovationen begleiten wir die öffentliche Hand in die digitalisierte Zukunft.
Das Unternehmen
Erfahren Sie mehr über unsere Anfänge, Werte und Innovationen. Immer einen Schritt voraus zu sein, zeichnet uns als verlässlichen Transformationspartner aus.
Projekte
Seit über 15 Jahren setzen wir mit unserer Expertise und Erfahrung Projekte deutschland- und EU-weit erfolgreich um.
Im ländlichen Raum das volle Potenzial für Wirtschaft und Gesellschaft ausschöpfen – mit nachhaltigen Infrastrukturen.
Ob Evaluation des Ist-Zustandes, Strategieentwicklung oder Umsetzung von Digitalisierungsprojekten – wir unterstützen bei der digitalen Transformation.
Mit individuellen Lösungen und nachhaltigen Innovationen begleiten wir die öffentliche Hand in die digitalisierte Zukunft.
Erfahren Sie mehr über unsere Anfänge, Werte und Innovationen. Immer einen Schritt voraus zu sein, zeichnet uns als verlässlichen Transformationspartner aus.
Seit über 15 Jahren setzen wir mit unserer Expertise und Erfahrung Projekte deutschland- und EU-weit erfolgreich um.
Zukunft ist immer. aconium.
Die aconium GmbH aus Berlin begleitet den öffentlichen Sektor bei der Projektentwicklung in den Bereichen Digitalisierung, Energie, Mobilität, Gesundheit und Bildung.
Wir bringen Kommunen, Landkreise und Unternehmen zusammen und entwickeln gemeinsam die Infrastruktur für die Zukunft. Die Stärkung des ländlichen Raums steht im Fokus unserer Arbeit.
Mit deutschen und europäischen Partnern arbeiten wir an Förderprojekten beispielsweise zur Digitalisierung des ländlichen Raums, entwickeln smarte Mobilitätskonzepte für den Nah- und Regionalverkehr oder intelligente Strategien, um die Energiewende voranzubringen. Zudem ist aconium als Projektträger des Förderprogramms für den Ausbau des Gigabit-Internets im Auftrag des Bundesministeriums für Digitales und Verkehr tätig.
Global
aufgestellt
Erfolgsgeschichten schreiben wir gemeinsam. Mit mehr als 400 Mitarbeitenden gehört die aconium GmbH zu den Top 100 der innovativsten Mittelständler in Deutschland. Wir leben Innovation. Wir überzeugen mit Kompetenz. Wir gestalten zusammen. Europaweit – seit mehr als 15 Jahren.
aconium hat in Deutschland neben der Berliner Zentrale sieben Regionalbüros: Düsseldorf, Leipzig, München, Osterholz-Scharmbeck bei Bremen, Schwerin, Stuttgart und Wiesbaden. Zudem verfügen wir über Standorte in Brüssel, Kiew und Tirana.
aconium
Produktwelt
Die Digitalisierung erfordert effiziente Prozesse und intelligente Anwendungen für erfolgreiches Projekt- und Fördermanagement sowie für die moderne Verwaltung. Mit eigenentwickelten, anpassbaren digitalen Lösungen unterstützen wir die tägliche Arbeit für eine effiziente Regionalentwicklung.
Über 450 Seiten Breitbandwissen
Kommunen stehen beim Breitbandausbau vor einer komplexen Herausforderung. Unsere Loseblattsammlung hilft, diese zu erkennen und zu bewältigen.
Der aconium Newsletter
Neuigkeiten, Infos und hilfreiche Artikel aus den Bereichen Digitalisierung, Energie, Mobilität, Gesundheit und Bildung.
aconium Funds - Fördermittel-App
Sie sind auf der Suche nach Fördermöglichkeiten für Ihr Projekt? Mit unserer App werden Sie fündig!

Über 450 Seiten Breitbandwissen
Kommunen stehen beim Breitbandausbau vor einer komplexen Herausforderung. Unsere Loseblattsammlung hilft, diese zu erkennen und zu bewältigen.

Der aconium Newsletter
Neuigkeiten, Infos und hilfreiche Artikel aus den Bereichen Digitalisierung, Energie, Mobilität, Gesundheit und Bildung.
Unsere
Partnerschaften
Projekte und Referenzen
Projekte geben neue Impulse, bringen Organisationen, Mitarbeitende und Kunden voran und können ein flexibles und zielgerichtetes Arbeiten ermöglichen. Die aconium GmbH macht dieses Arbeiten in Projekten in ganz Europa mit mehr als 14.500 Ansprechpersonen, Projektmitarbeitenden und Organisationen möglich.
Aktuelle Meldungen
Messen und Events
Branchendialog und Punktekompass sorgen für frühe Entscheidungsgrundlagen
Der Bund stellt auch in diesem Jahr Fördermittel für den Gigabit-Ausbau bereit. Um frühzeitig zu...
Aufruf zur Antragseinreichung zur Förderung von Beratungsleistungen für den Gigabitausbau
Das BMDV ermöglicht die Antragstellung für Beratungsleistungen für den Gigabitausbau in...
Messen und Events
Akteure und Stakeholder einbinden, gemeinsam Ideen für Transformationsprozesse entwickeln, Ergebnisse und Strategien präsentieren – kreative Veranstaltungsformate unterstützen dabei, Ideen und Vorhaben der Öffentlichkeit vorzustellen, Partizipation zu ermöglichen und zielführende Innovationsprozesse anzuschieben.
Aktuelle Meldungen
Branchendialog und Punktekompass sorgen für frühe Entscheidungsgrundlagen
Der Bund stellt auch in diesem Jahr Fördermittel für den Gigabit-Ausbau bereit. Um frühzeitig zu...
Aufruf zur Antragseinreichung zur Förderung von Beratungsleistungen für den Gigabitausbau
Das BMDV ermöglicht die Antragstellung für Beratungsleistungen für den Gigabitausbau in...
Messen und Events
Akteure und Stakeholder einbinden, gemeinsam Ideen für Transformationsprozesse entwickeln, Ergebnisse und Strategien präsentieren – kreative Veranstaltungsformate unterstützen dabei, Ideen und Vorhaben der Öffentlichkeit vorzustellen, Partizipation zu ermöglichen und zielführende Innovationsprozesse anzuschieben.